What is Porosity in Welding: Important Tips for Achieving Flawless Welds
What is Porosity in Welding: Important Tips for Achieving Flawless Welds
Blog Article
Porosity in Welding: Identifying Common Issues and Implementing Best Practices for Prevention
Porosity in welding is a pervasive issue that frequently goes unnoticed until it triggers considerable issues with the stability of welds. In this discussion, we will certainly discover the crucial elements adding to porosity formation, analyze its damaging effects on weld efficiency, and talk about the best methods that can be embraced to minimize porosity event in welding processes.
Common Reasons For Porosity

An additional frequent perpetrator behind porosity is the existence of contaminants externally of the base metal, such as oil, grease, or rust. When these impurities are not effectively eliminated prior to welding, they can vaporize and come to be trapped in the weld, triggering issues. Using filthy or damp filler materials can present pollutants right into the weld, contributing to porosity problems. To reduce these common reasons of porosity, thorough cleansing of base steels, proper protecting gas choice, and adherence to optimum welding parameters are vital techniques in attaining top quality, porosity-free welds.
Impact of Porosity on Weld High Quality

The presence of porosity in welding can considerably compromise the structural honesty and mechanical buildings of bonded joints. Porosity produces gaps within the weld metal, deteriorating its general toughness and load-bearing capability. These gaps function as anxiety focus factors, making the weld more at risk to cracking and failing under applied loads. Additionally, porosity can reduce the weld's resistance to rust and other environmental aspects, even more lessening its longevity and efficiency.
Welds with high porosity degrees often tend to display lower impact stamina and minimized capacity to flaw plastically prior to fracturing. Porosity can impede the weld's capability to effectively send pressures, leading to premature weld failing and prospective safety risks in vital frameworks.
Ideal Practices for Porosity Avoidance
To enhance the architectural honesty and quality of bonded joints, what specific procedures can be implemented to lessen the event of porosity throughout the welding procedure? Using the right welding technique for the details product being bonded, such as changing the welding angle and weapon setting, can even more prevent porosity. Routine assessment of welds and immediate remediation of any kind of problems identified during the welding process are vital techniques to prevent porosity and produce top quality welds.
Value of Proper Welding Methods
Executing correct welding techniques is paramount in making sure the architectural stability and top quality of bonded joints, building upon the foundation of efficient porosity prevention actions. Welding techniques straight influence the overall toughness and resilience of the bonded structure. One essential element of correct welding strategies is keeping the appropriate warm input. Too much heat can cause increased porosity as a result of the entrapment of gases in the weld swimming pool. On the other hand, insufficient heat may cause incomplete blend, producing possible weak factors in the joint. Furthermore, using the proper welding specifications, such as voltage, existing, and travel rate, is essential What is Porosity for attaining sound welds with very little porosity.
Additionally, the selection of welding process, whether it be MIG, TIG, or stick welding, should line up with the details demands of the task to guarantee optimum outcomes. Correct cleansing and preparation of the base steel, in addition to selecting the appropriate filler material, are likewise vital parts of competent welding methods. By sticking to these best techniques, welders can minimize the threat of porosity formation and create top quality, structurally sound welds.
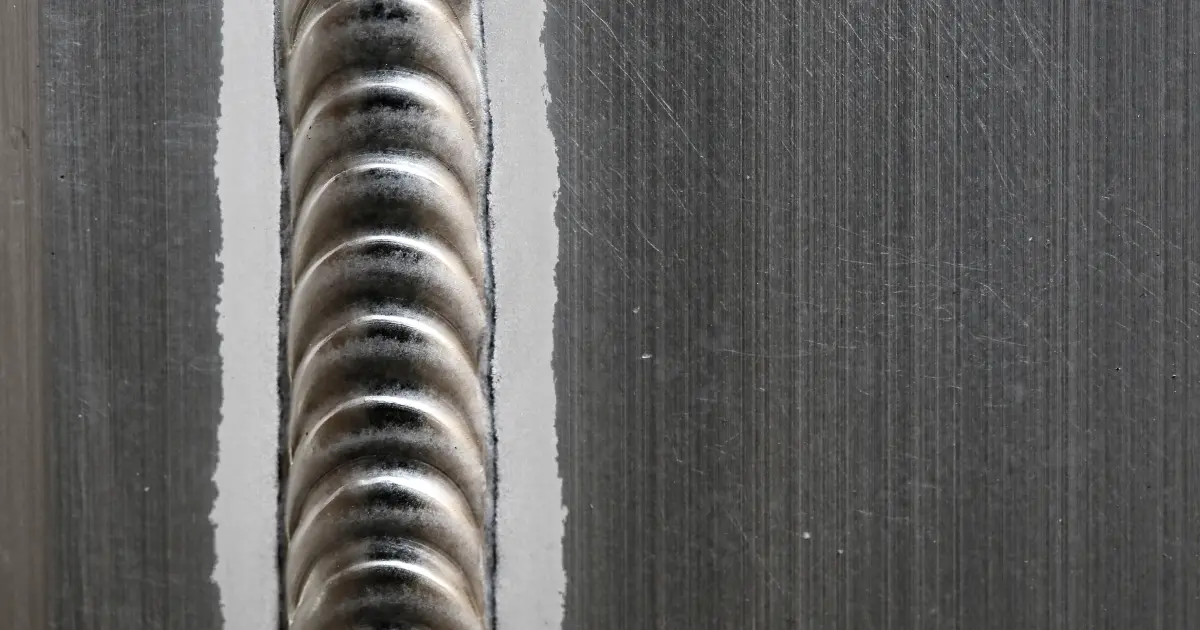
Testing and Quality Assurance Steps
Quality assurance procedures play a vital duty in verifying the stability and visit site integrity of welded joints. Testing treatments are necessary to spot and stop porosity in welding, ensuring the toughness and longevity of the end product. Non-destructive testing techniques such as ultrasonic testing, radiographic testing, and aesthetic inspection are commonly used to determine possible flaws like porosity. These techniques enable the analysis of weld top quality without endangering the honesty of the joint. What is Porosity.
Post-weld inspections, on the other hand, evaluate the last weld for any type of issues, including porosity, and verify that it satisfies specified criteria. Applying a detailed quality control plan that consists of thorough screening procedures and inspections is critical to minimizing porosity concerns and making sure the total high quality of welded joints.
Conclusion
To conclude, porosity in welding can be a common concern that affects the quality of welds. By identifying the usual root causes of porosity and implementing best methods for avoidance, such as proper welding techniques visit site and testing steps, welders can make certain high top quality and trusted welds. It is important to prioritize avoidance methods to reduce the incident of porosity and preserve the integrity of bonded frameworks.
Report this page